Mécanique
L'AUV 7 a un grand volume et l'espace intérieur n'est pas organisé. La fibre de carbone était innovante, mais elle était plus légère que prévu. Par conséquent, la densité du sous-marin est trop faible et il devient difficile pour lui de plonger. Pour surmonter ce défi, l'équipe mécanique a ajouté 25 livres de ballasts afin de réduire la flottabilité. L'un des objectifs de cette année avec la nouvelle conception du sous-marin est de réduire les pénalités de poids. Avec le nouveau sous-marin, le design est beaucoup plus petit afin d'augmenter sa densité. De cette façon, aucune masse inutile n'a été ajoutée. Même si le sous-marin était plus petit, il était important que tout le matériel existant puisse rentrer à l'intérieur, en raison de contraintes budgétaires et logistiques. L'équipe mécanique vise un poids total de 77 lb.
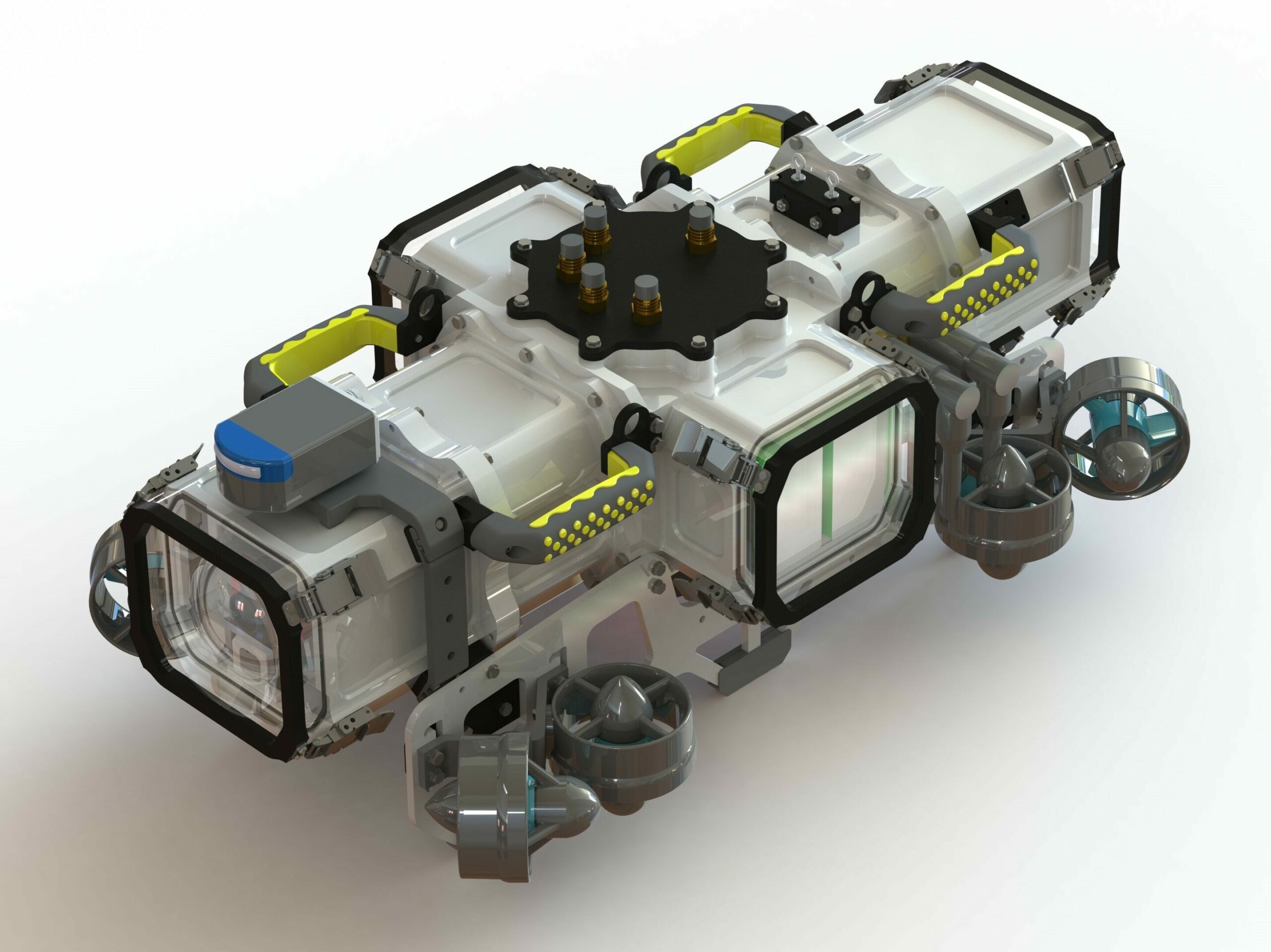
Avec deux sous-marins à entretenir, l'équipe mécanique doit être la plus réactive possible lorsque des problèmes de conception technique surviennent pendant la compétition. Par conséquent, il était clair que l'accessibilité des composants devait être l'objectif principal de la nouvelle conception. L'équipe a décidé d'augmenter le nombre de points d'accès en plus d'augmenter leur taille. L'intérieur est entièrement creux sans obstruction interne, telle que des cercles de boulons internes. Un système de clip a été ajouté pour éviter à l'équipe d'avoir à visser des composants à l'intérieur du sous-marin. Pendant la compétition, cette pièce est vitale puisqu'elle permet à l'équipe de sortir toutes les pièces critiques rapidement et sans outillage spécifique.
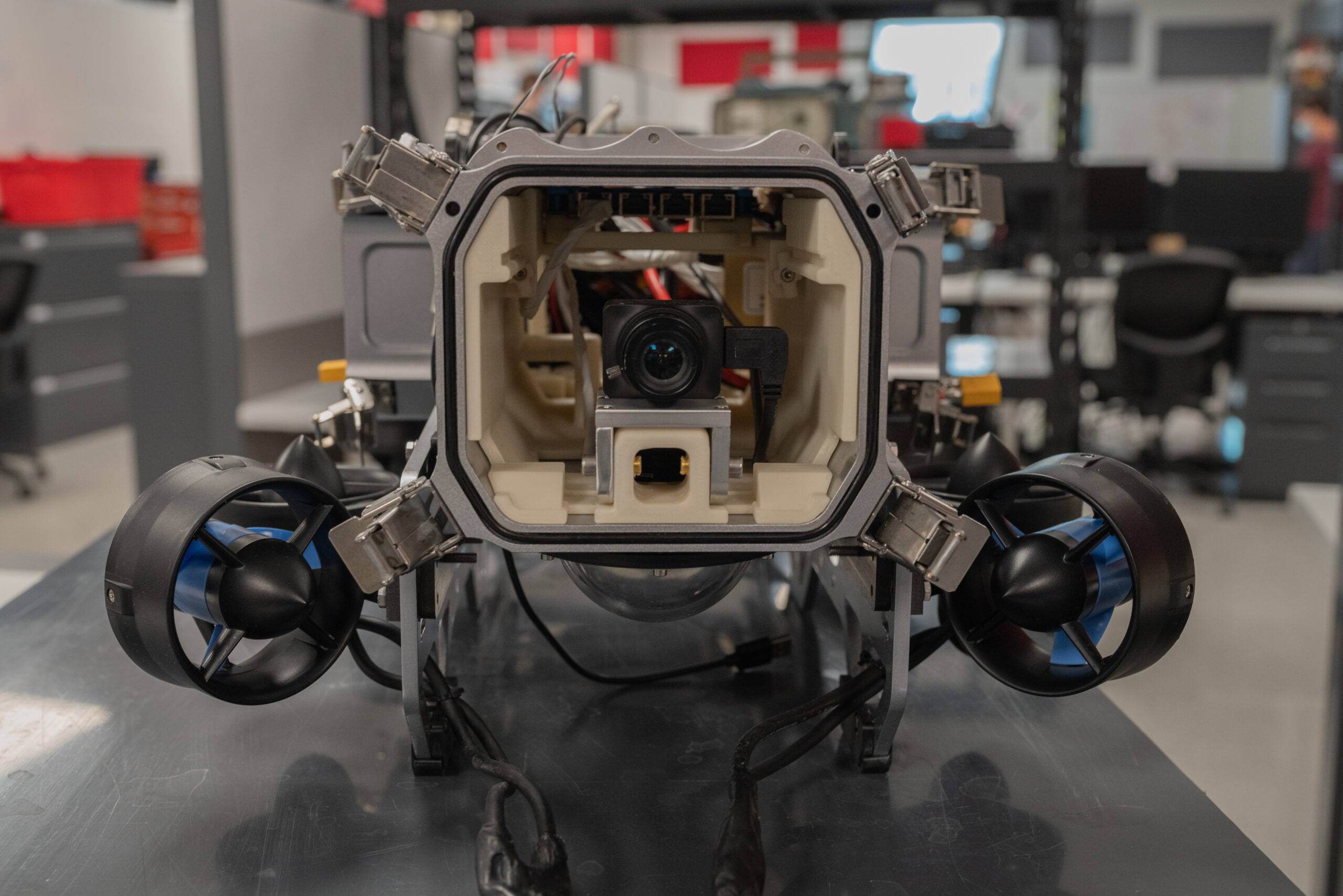
Avec le nouveau design, l'équipe a décidé d'opter pour une coque entièrement en aluminium après quelques délibérations. Premièrement, la matière première est moins chère et plus facile à fabriquer que la fibre de carbone. Deuxièmement, avec l'aluminium, l'échange de chaleur du sous-marin à l'eau sera meilleur que la coque en fibre de carbone. La plupart des pièces ont été programmées et usinées par l'équipe mécanique. Il a été décidé d'anodiser le nouvel AUV-8 pour le protéger au fil des années. Une couleur claire a été choisie comme protection supplémentaire et pour réduire l'échauffement du sous-marin hors de l'eau.
Pour l'intérieur, l'équipe mécanique a conçu la plupart des supports pour qu'ils soient imprimés en 3D. L'objectif principal de ces derniers est qu'ils ne nécessitent aucune fixation ni aucun outil pour le montage et le démontage. Ces supports peuvent être démontés rapidement pour aider les membres de l'équipe électrique à déboguer un dysfonctionnement électrique pendant la compétition. Le principal défi est d'adapter tous les gros composants, tels que le Jetson Xavier et le DVL, en maintenant l'accès et l'amovibilité à l'intérieur de la coque. Une conception et des tests minutieux ont permis de garantir que tout s'emboîte sans accrocs.
Électrique
Avec la nouvelle conception mécanique, toute la plate-forme électrique a dû être repensée. Le premier objectif des membres de l'équipe était de résoudre les problèmes de la plate-forme précédente sans augmenter le travail de l'équipe logicielle. Les nouvelles cartes personnalisées de l'AUV-8 utilisent le même protocole de communication précédemment utilisé sur l'AUV 7.
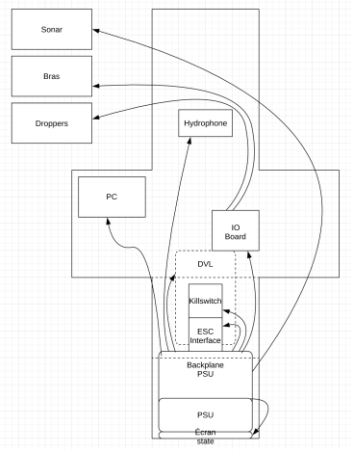
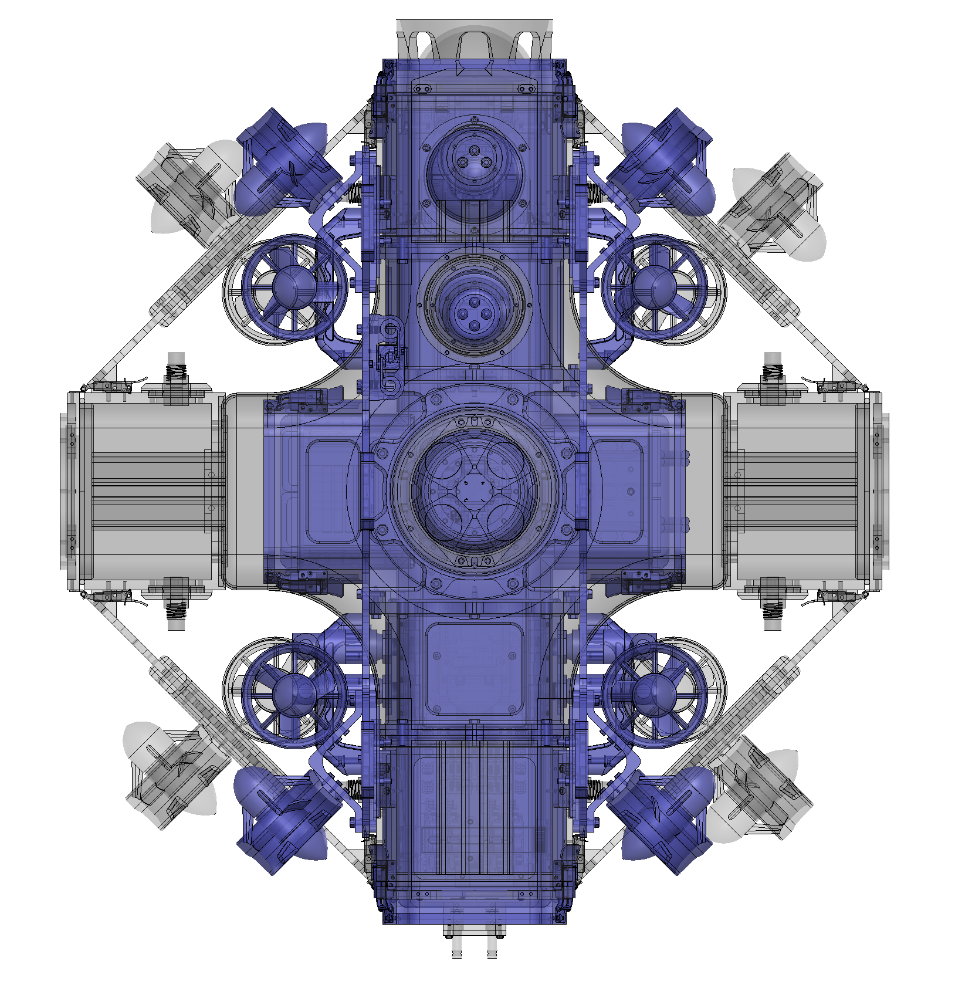
Le changement majeur sur le nouveau prototype est sa taille. Étant donné que le nouveau sous-marin est considérablement plus petit en volume, le PCB devait être de conception plus petite. La carte d'alimentation devait s'adapter à la nouvelle conception d'extrusion avec une réduction de sa taille de 40% sans compromettre la puissance délivrée à l'ESC tout en utilisant les propulseurs avec une meilleure efficacité. L'alimentation doit encore fournir deux canaux d'alimentation pour l'ESC et un canal qui convertit le 16V des batteries en 12V. L'objectif d'une autre équipe était de changer le capteur de courant et de tension.
Sur l'AUV-7, l'équipe n'a pas pu utiliser ces capteurs. Les membres ont changé les capteurs analogiques pour un capteur numérique qui communique avec le protocole I2C. Les capteurs INA226 sont utilisés pour surveiller le courant et la tension de l'ESC et pour le convertisseur 12V. L'objectif principal de ce projet est de pouvoir avoir un meilleur retour sur l'état électrique et la consommation du sous-marin pour améliorer son contrôle.
Logiciel
S.O.N.I.A. a ajouté CI/CD sur le processus de développement. Pour ce faire, nous avons migré des messages et des services ROS personnalisés dans un seul package. En l'utilisant comme base, cela ajoute plus de vingt images Docker contenant un package qui contrôle un aspect du sous-marin (contrôle, propulseur, sonar, etc.). Avec l'ajout de Docker, l'environnement de développement est uniforme pour tous les membres de l'équipe. Le débogage et le test des différents composants du logiciel sont plus faciles.
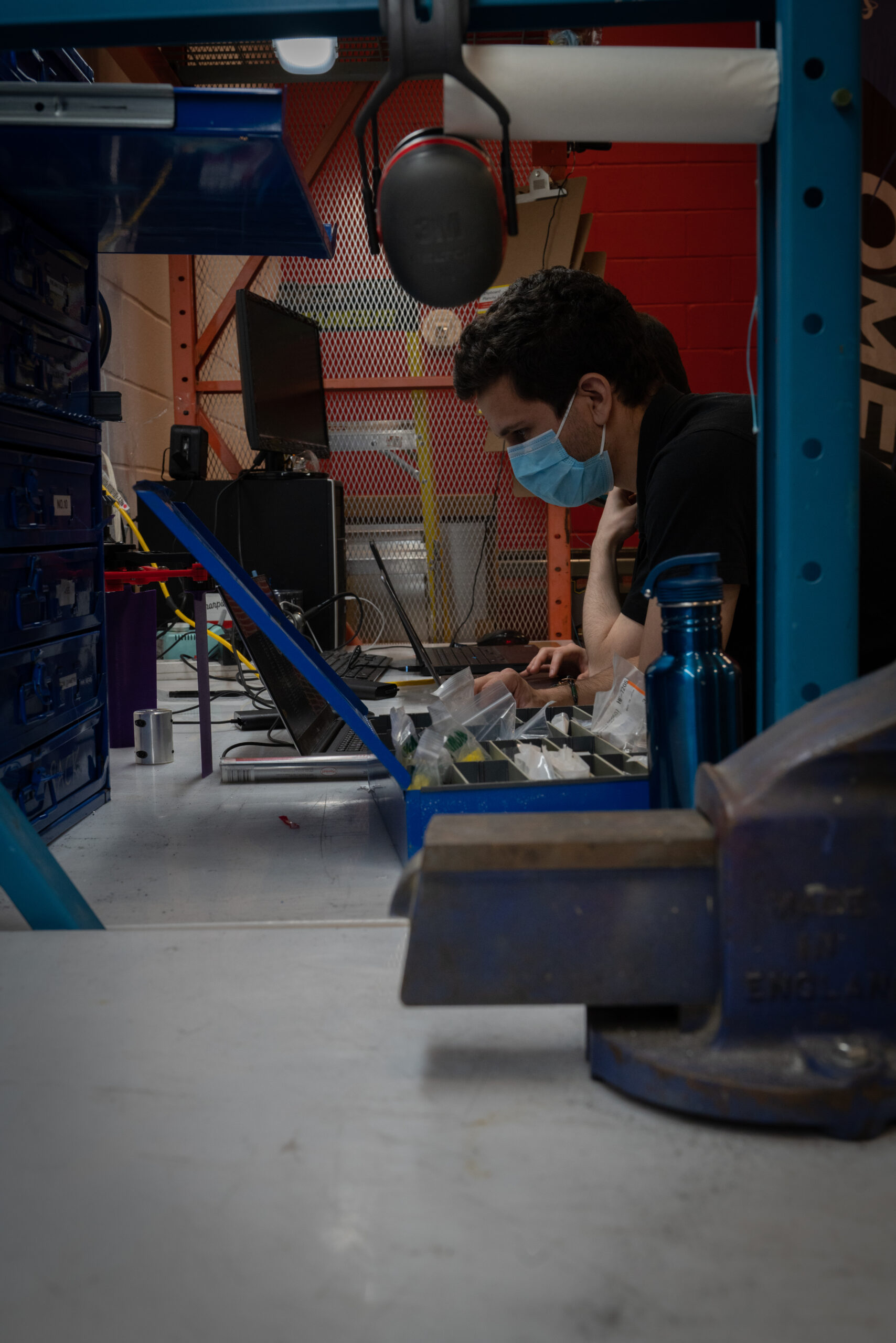
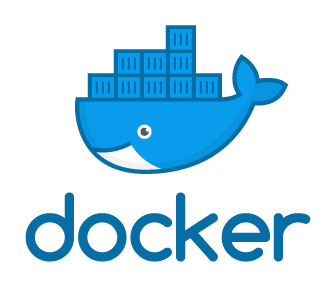
Les conteneurs peuvent également être débogués directement sur le sous-marin, à l'aide de l'extension Visual Studio Code Remote Container. L'équipe a fait le choix d'utiliser GitHub Actions comme CI/CD pour créer des images Docker lorsque les commits sont poussés sur GitHub. Ces images sont tirées sur le sous-marin et sont prêtes à être exécutées (il n'y a plus de C++ ou Python déployé directement sur le sous-marin, seul conteneur contenant chaque module).
Galerie
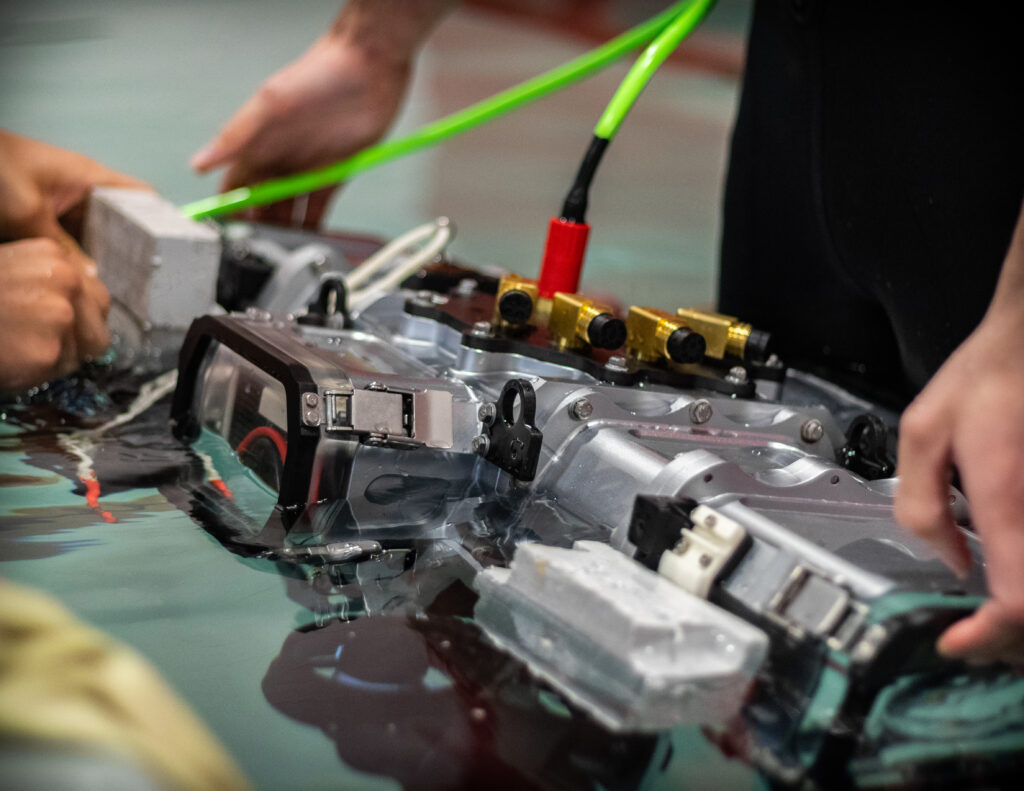
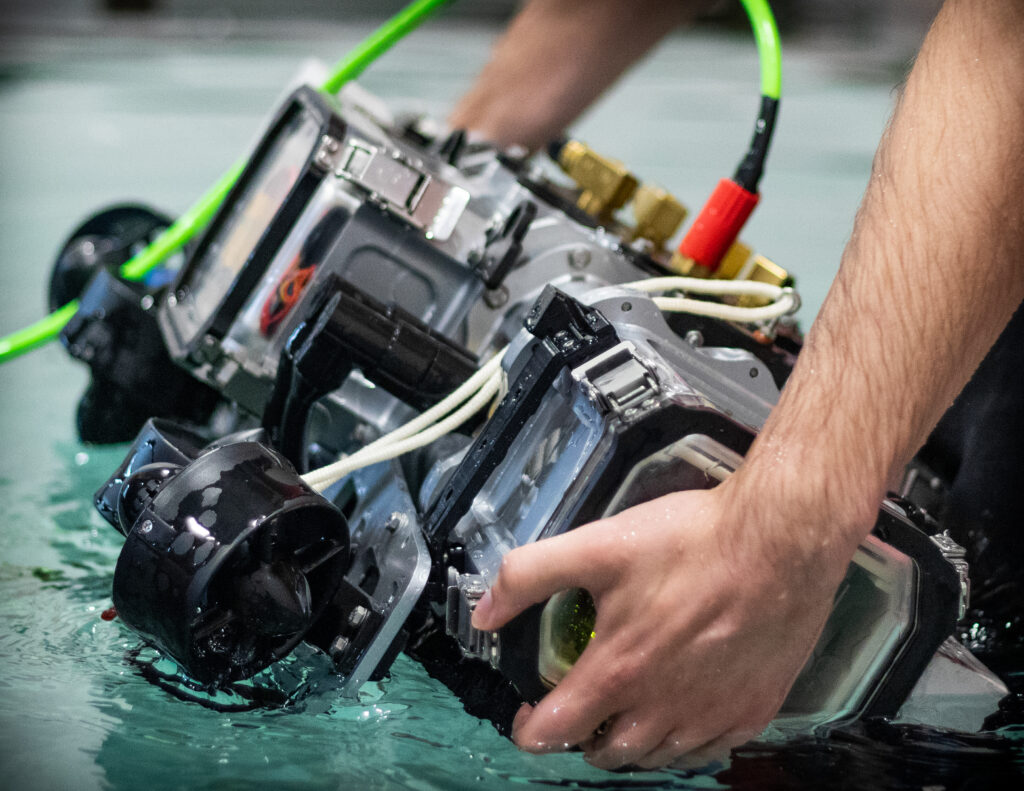
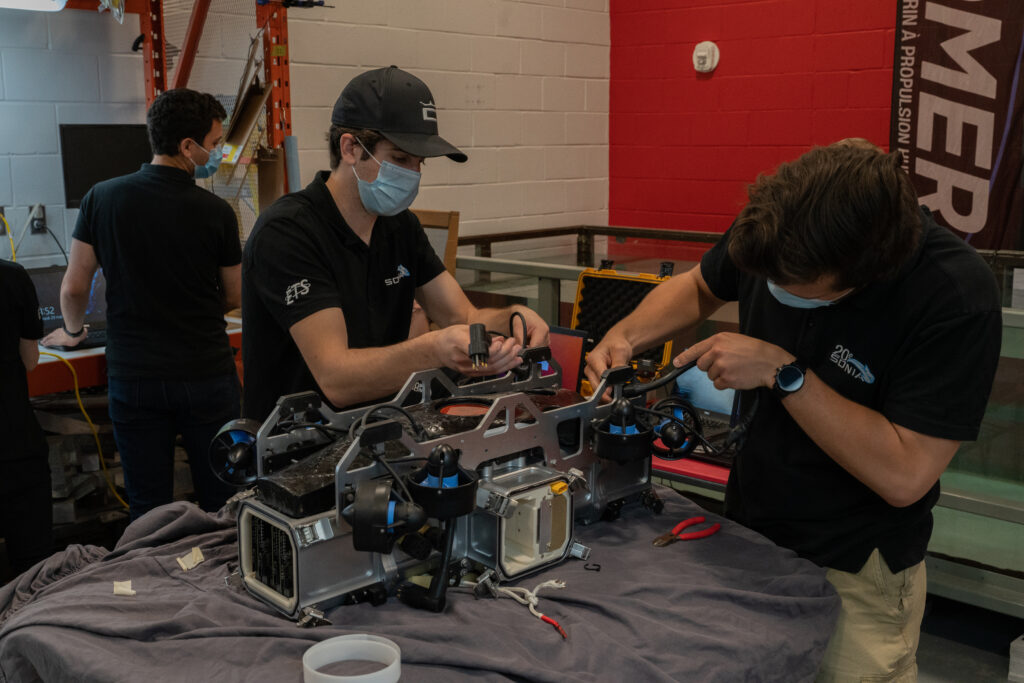
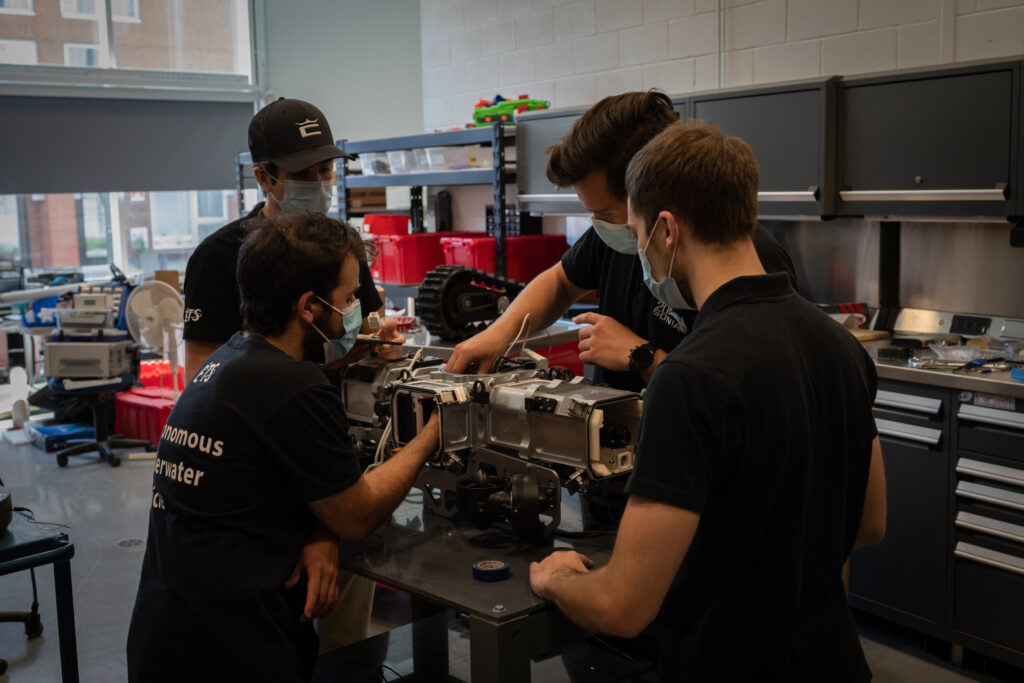
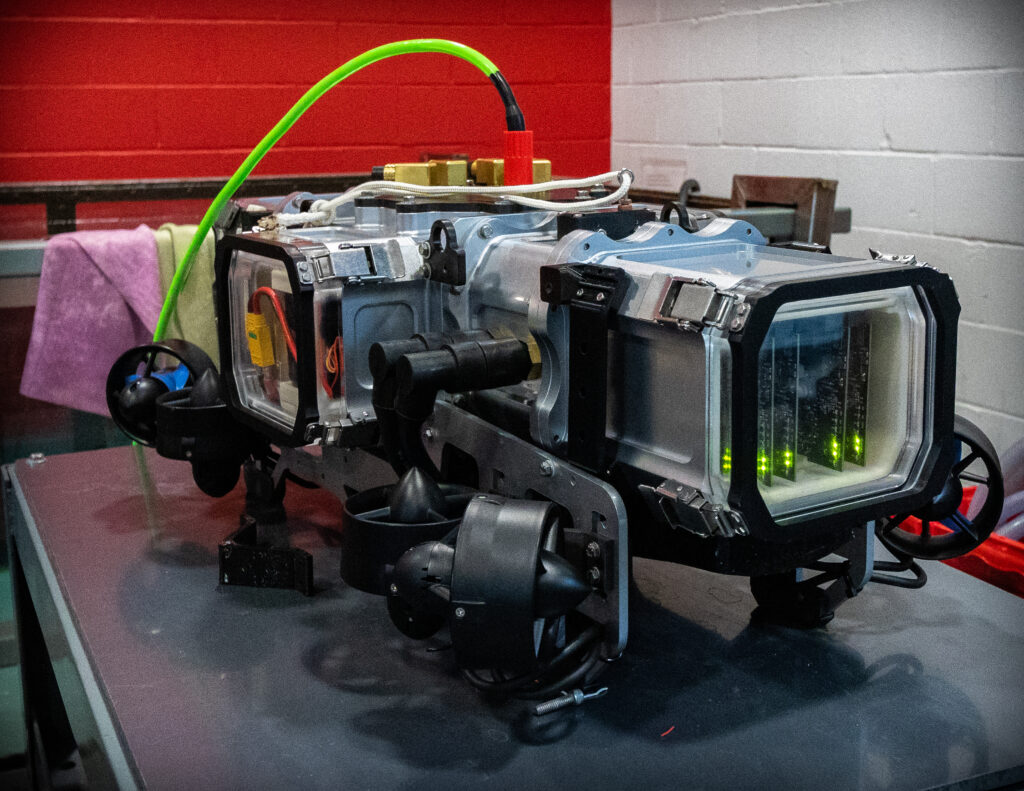
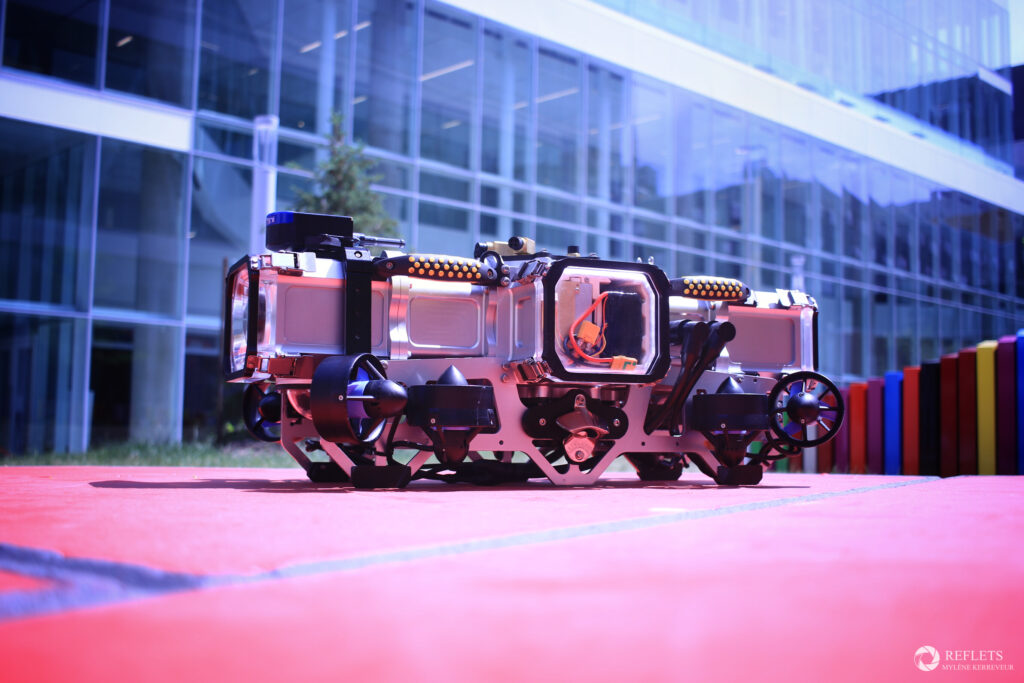
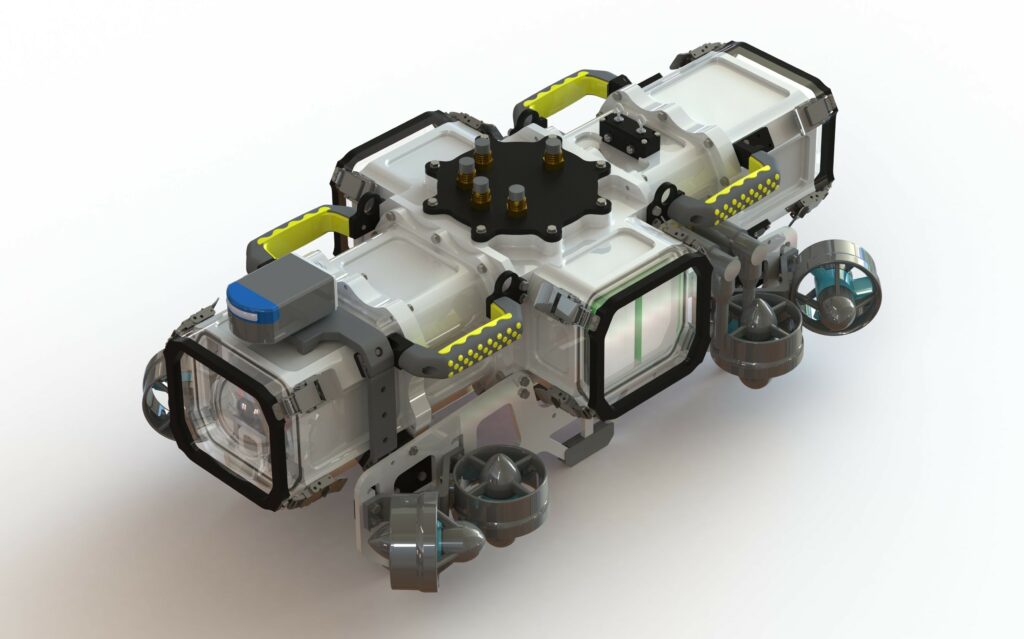
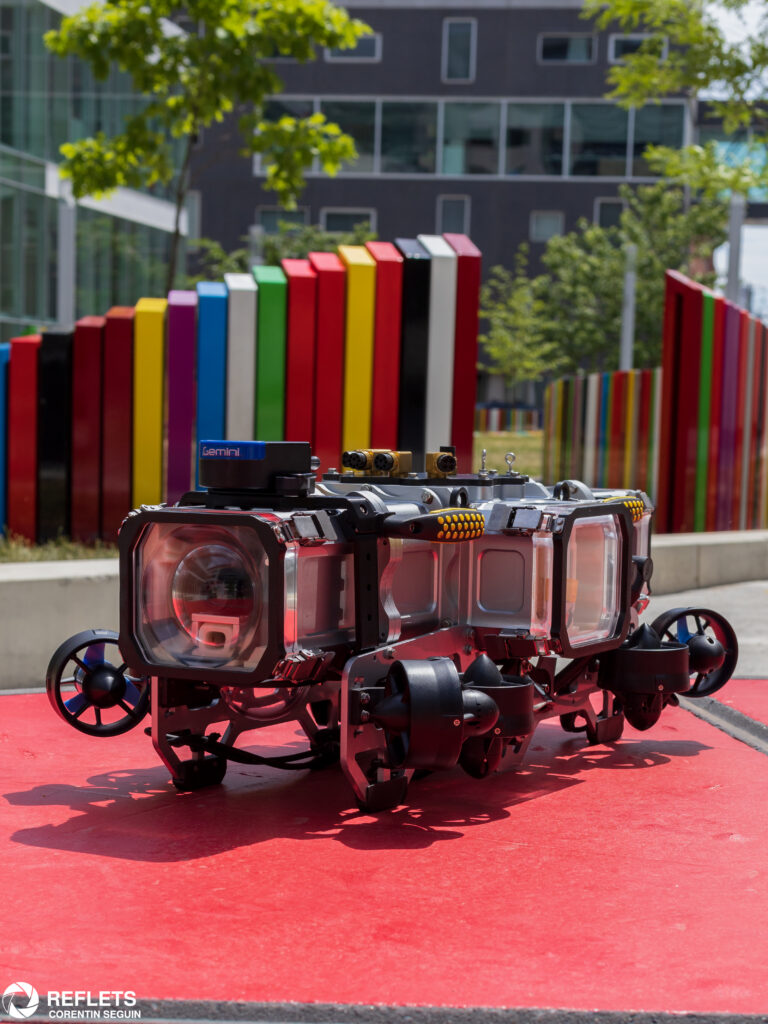
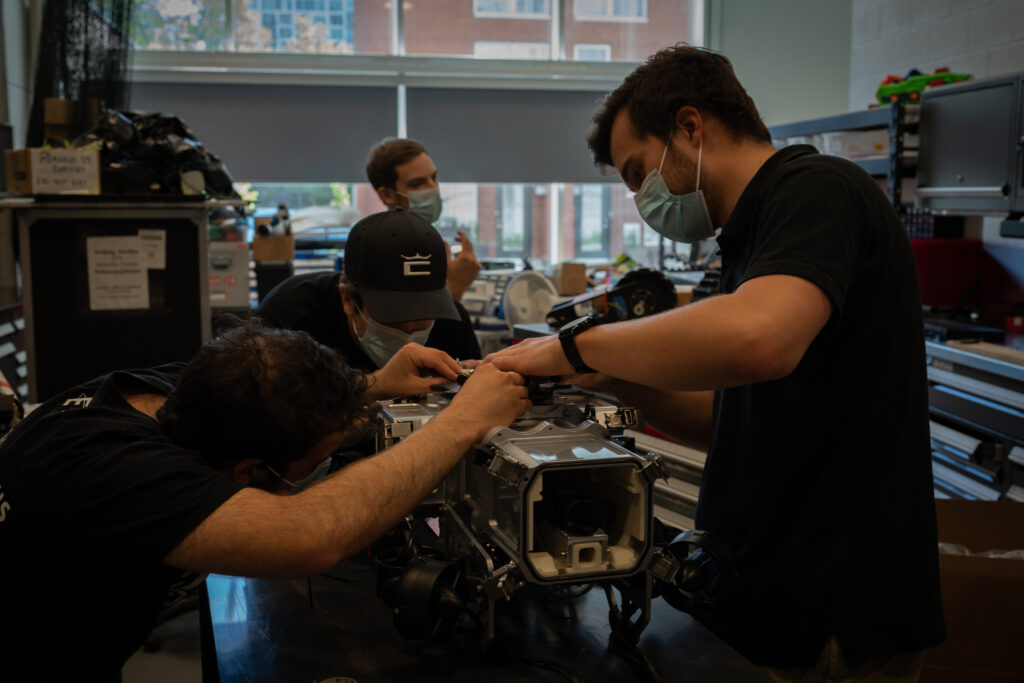
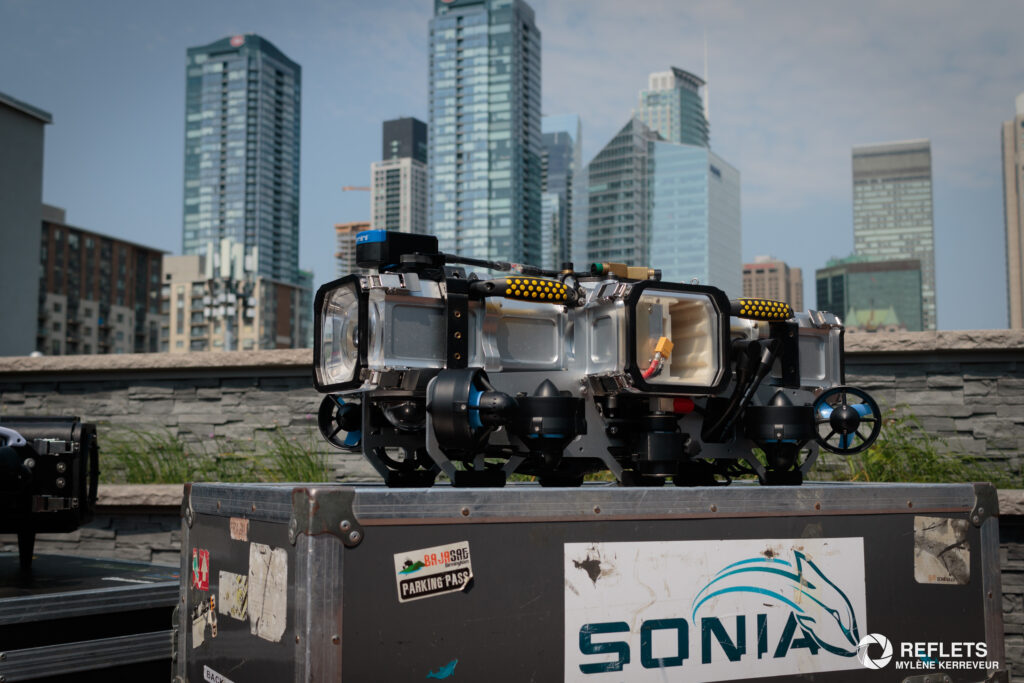
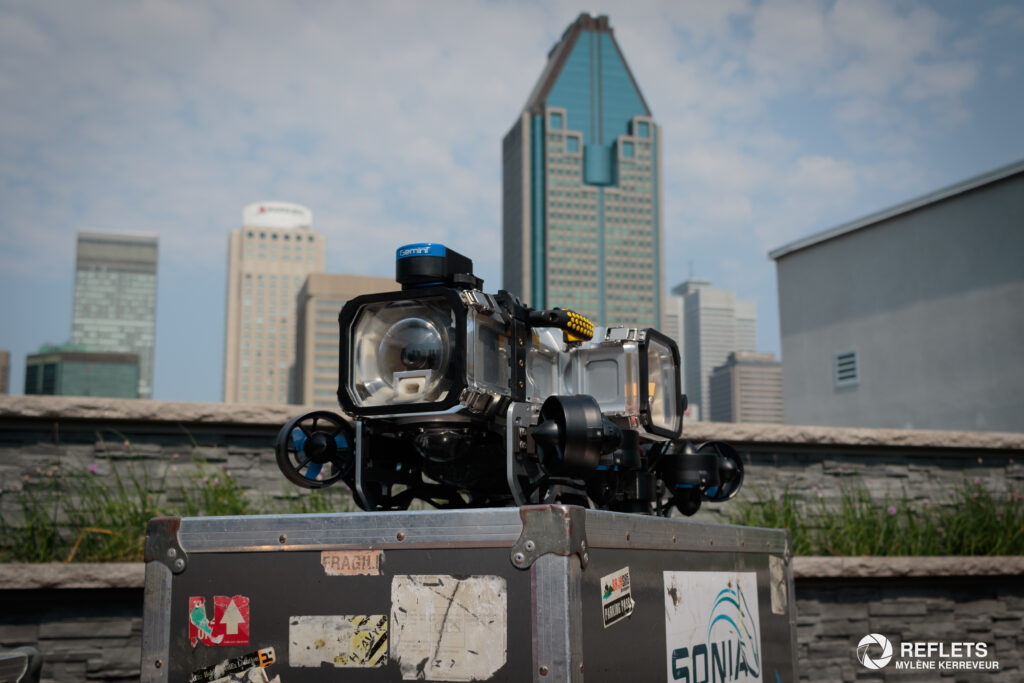