Mécanique
Concernant l'aspect mécanique de l'AUV 7, les membres ont décidé de le façonner en croix pour permettre un meilleur contrôle sur celui-ci ainsi que de faire des hypothèses mathématiques sur sa conception car il est vraiment symétrique à la fois sur l'axe x et sur l'axe y. Un autre avantage du corps en croix est qu'il permet une meilleure répartition des composants sur les quatre bras ainsi qu'un changement plus facile de la configuration des instruments. La partie principale de la coque est compacte, creuse et est en fibre de carbone. Cela laisse plus d'espace interne au centre du sous-marin pour placer des composants électroniques ainsi que des ballasts pour l'équilibrage statique du sous-marin.
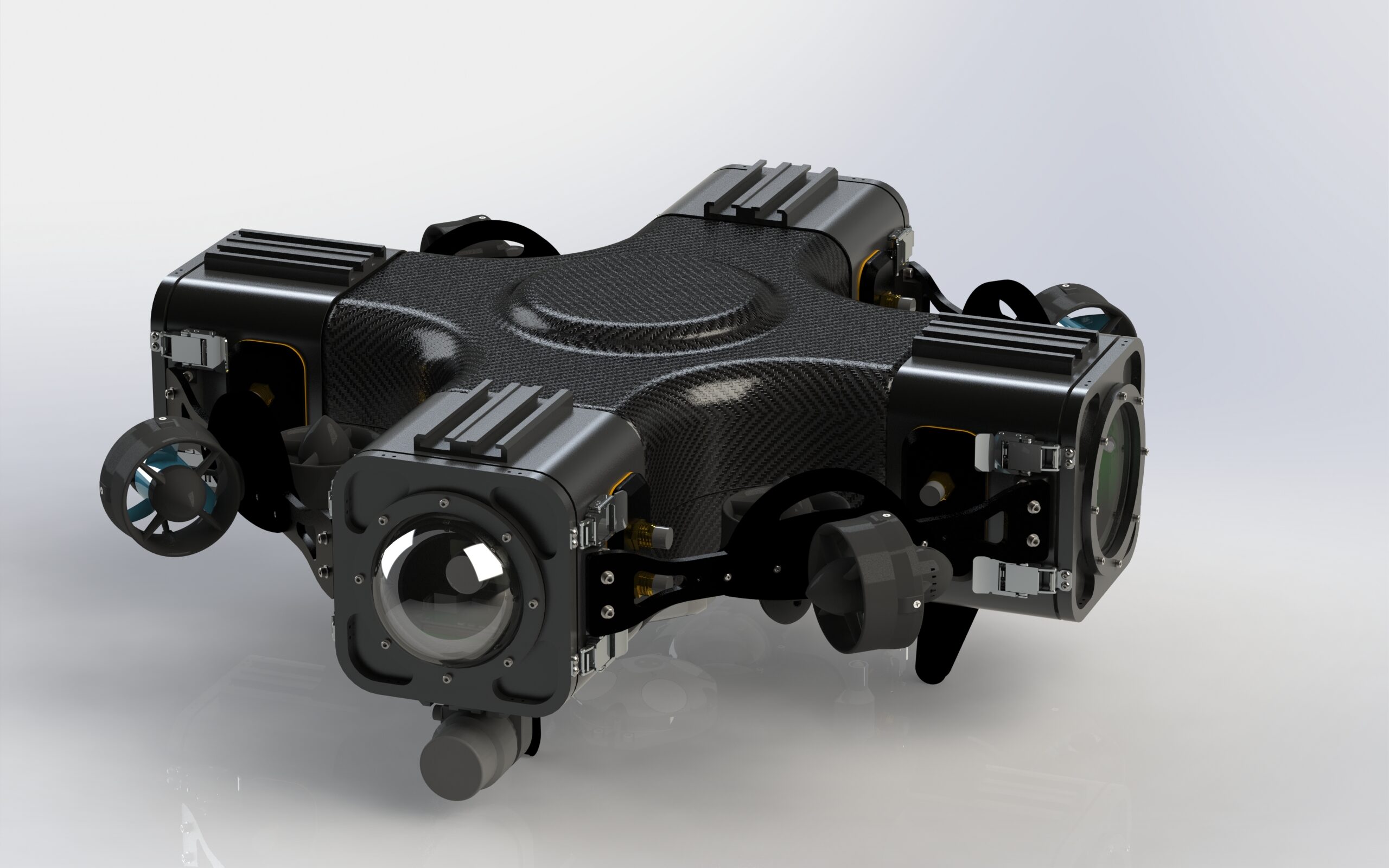
La conception de la coque a été déterminée pour optimiser l'espace pour les composants, permettre un accès plus facile à ceux-ci, et avoir un meilleur contrôle sur la position des plaques de ballast utilisées pour gérer le centre de gravité. Les bras ont été conçus pour permettre une insertion et un retrait faciles de l'électronique qu'ils contiennent et, tout aussi important, une gestion efficace de la chaleur de ceux-ci.
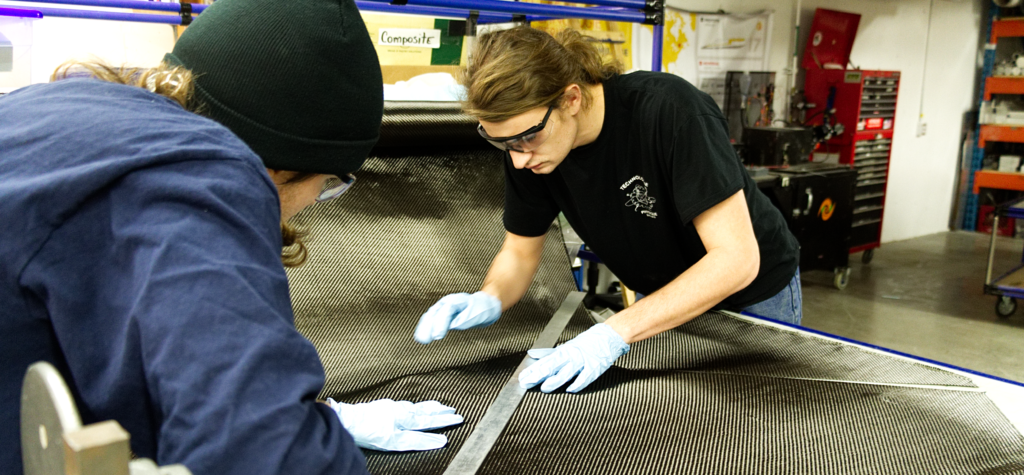
Le choix de la fibre de carbone pour construire la partie principale de la coque a été fait pour réduire le gaspillage des matériaux utilisés dans le processus de fabrication. En effet, fabriquer la coque creuse en aluminium aurait nécessité de mâcher la majeure partie de la matière première ainsi qu'un assemblage en deux parties. L'utilisation d'un matériau composite a permis une utilisation beaucoup plus efficace du matériau et une plus grande taille interne en raison des fortes propriétés structurelles de la fibre de carbone qui ont permis une construction plus fine de la coque par rapport à une construction en aluminium avec la même taille externe. Cet espace interne amélioré permet une meilleure gestion des câbles.
Cependant, l'équipe a réussi à réaliser cette pièce en passant par quelques essais. En effet, la première fois, la coque était constituée de quatre couches de fibre de carbone qui s'avéraient trop fragiles pour conserver une structure principale rigide et résister à la pression exercée par l'eau. L'essai suivant a été fait en utilisant deux moitiés composées de six couches et, après que ces moitiés aient été collées ensemble à leur bride de rencontre, semblaient fournir une rigidité structurelle suffisante pour le sous-marin, mais ce n'était pas le cas. Le centre de forme ronde, hébergeant le Doppler Velocity Log (DVL) et une caméra, s'effondrerait lorsqu'une pression y serait appliquée. Pour remédier à ce problème, l'équipe mécanique a renforcé le centre de la coque en concevant et imprimant en 3D deux plaques en plastique qui reçoivent quatre tiges filetées qui poussent vers l'extérieur sur la coque à l'aide d'écrous. Bien que le renfort ronge un peu d'espace dans la coque, les tiges ont fini par être aussi le support sur lequel le lest est fixé, transformant le problème en solution.
Les quatre bras de la croix sont constitués de quatre blocs d'aluminium qui ont été usinés par l'un des membres de l'équipe, à l'aide d'une machine à commande numérique par ordinateur (CNC), et anodisés pour une protection supplémentaire. Ceux-ci sont essentiels pour la gestion de la chaleur de l'AUV car l'ordinateur et l'alimentation dégagent beaucoup de chaleur. Chacune des extrémités des bras se termine par un capuchon qui permet un accès facile aux composants que contient le bras.
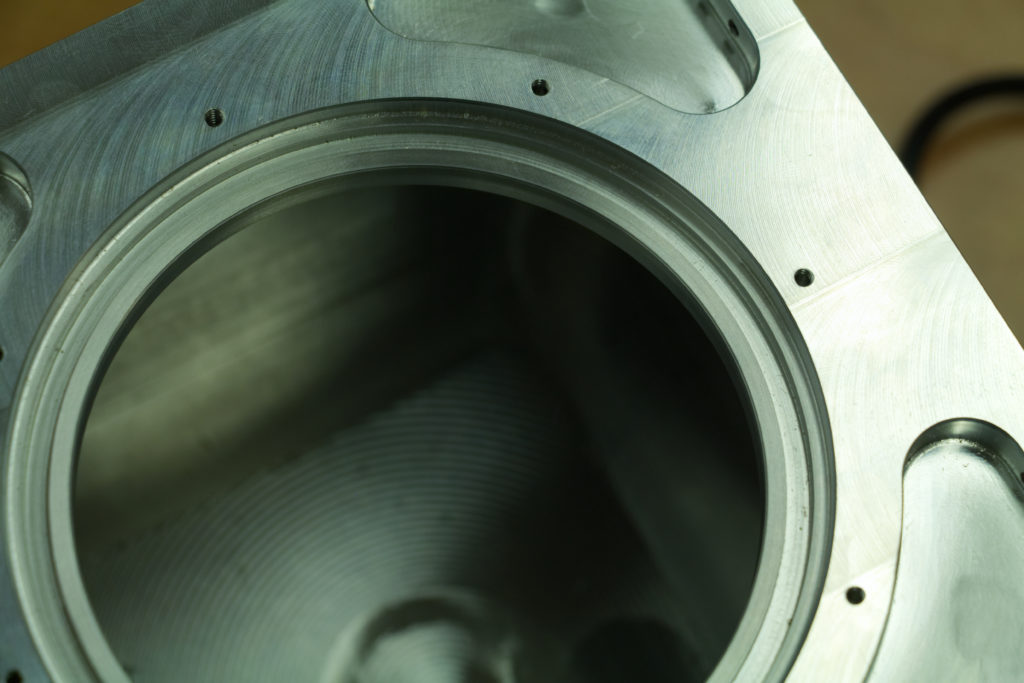
De plus, l'équipe a opté pour des rainures en T pour prendre en charge les divers instruments fixés à l'extérieur de la coque, car ils sont compatibles avec de nombreux matériaux standards. Ils permettent donc différentes configurations ainsi que l'utilisation d'outillage standard pour ajouter ou retirer les instruments. Quant aux torpilles, elles sont autopropulsées par un moteur électrique qui résout instantanément les problèmes causés par le système pneumatique encombrant utilisé sur la conception précédente car il n'est plus nécessaire.
Électrique
Concernant l'aspect électrique du sous-marin, l'objectif avec le nouveau design était d'avoir une connaissance approfondie de la technologie utilisée par l'AUV. Avec le roulement des membres de l'équipe, la compréhension des subtilités de l'ancien système s'est perdue. De plus, les contraintes mécaniques du nouveau concept rendaient l'ancienne électronique inadaptée tandis que l'ajout de deux moteurs, pour un total de huit, augmentait la charge au-delà de ce que les cartes d'alimentation pouvaient supporter.
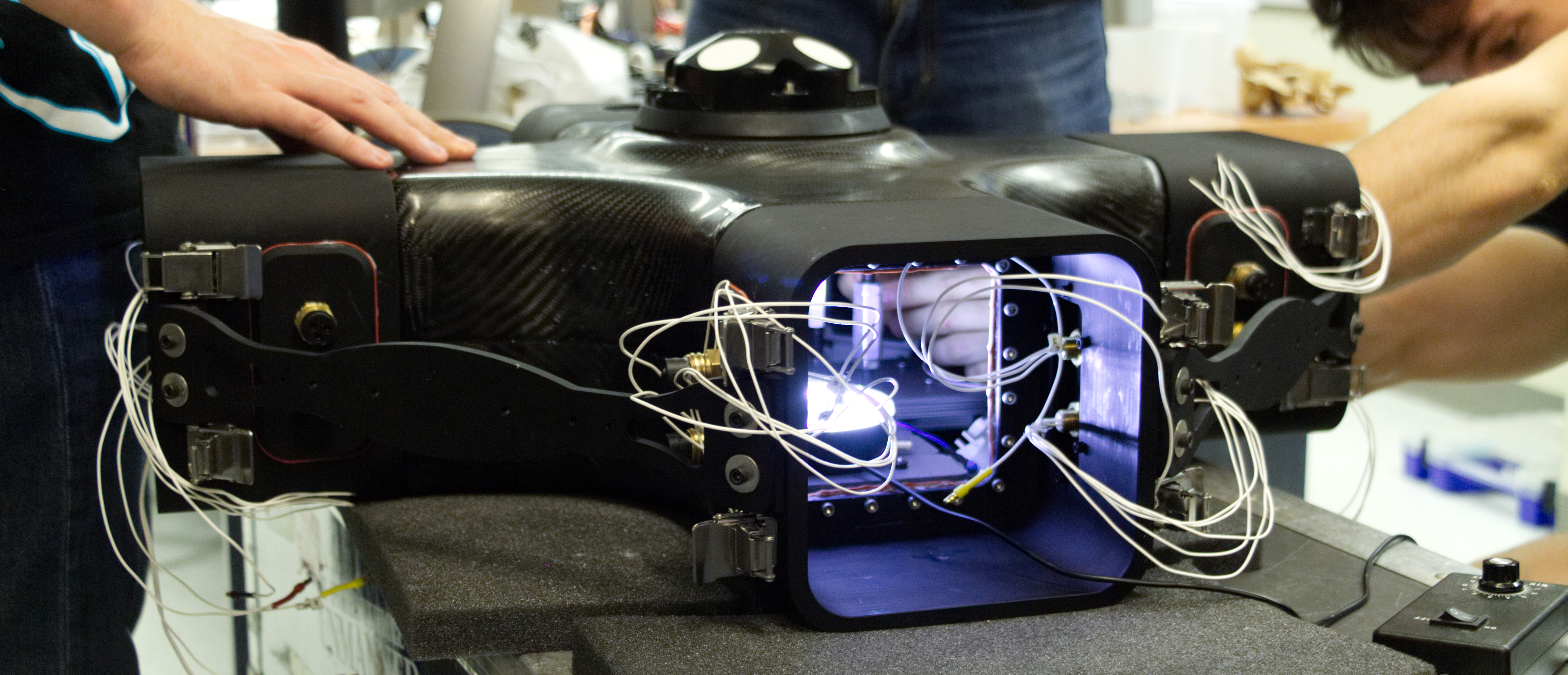
Les deux batteries du dernier AUV sont des batteries 4S, qui ont une tension nominale de 14,8V, qui, malgré une capacité inférieure à celle des anciennes batteries 7S (25,9V), sont plus adéquates pour les moteurs sans brosse. En effet, avec les batteries 4S, il n'est pas nécessaire de baisser la tension des moteurs. Chaque carte d'alimentation alimentant les moteurs possède deux voies de même tension nominale que la batterie. Chacun de ces canaux contrôle un moteur et peut être activé ou désactivé à l'aide d'un transistor Mosfet de type N. Un troisième canal d'alimentation a été développé avec une alimentation à découpage, plus précisément un convertisseur abaisseur, pour fournir 12V à l'ordinateur et au DVL. Sur chaque carte d'alimentation, le système contrôle l'ouverture des canaux ainsi que la surveillance de la température, du courant dans les canaux et de la tension des batteries et des canaux.
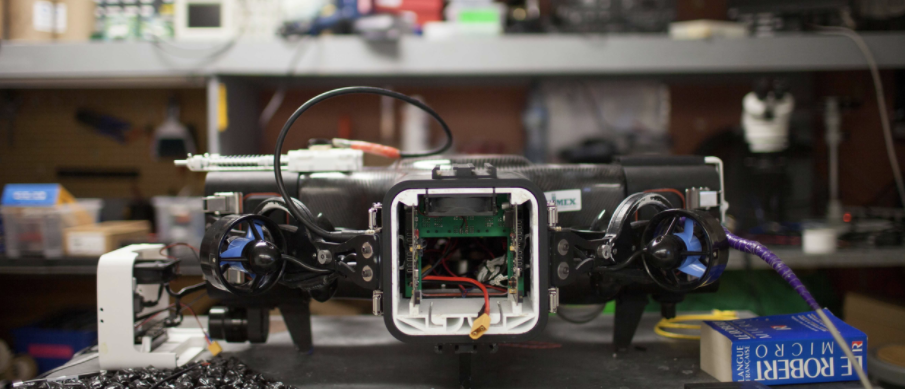
Le protocole de communication utilisé s'appuyait sur un réseau CAN. Au lieu de cela, le nouvel AUV utilise un réseau RS-485 en duplex intégral entre les 14 appareils. Ce protocole a été développé par l'un des membres de l'équipe et est spécialement conçu pour notre application afin d'optimiser l'utilisation de la bande passante et de gagner en flexibilité.
Sur l'AUV 7, les "backplanes" sont conçus pour faciliter l'interchangeabilité des composants pour pouvoir les modifier et les tester facilement. De plus, comme le nouveau design a moins de "backplanes" que l'ancien, il y a beaucoup plus de fils, ce qui rend la gestion des câbles plus difficile d'autant plus que la petite taille de la coque restreint l'accessibilité.
Logiciel
C'est le premier sous-marin qui a adopté le framework ROS. Auparavant, tous les modules étaient codés en utilisant Java et JAUS comme protocole de communication.
Sur ce schéma, chaque case carrée est un nœud, toutes les communications descendent vers les cases grises représentant les dispositifs externes, et leurs retours, ou données, remontent vers les niveaux décisionnels.
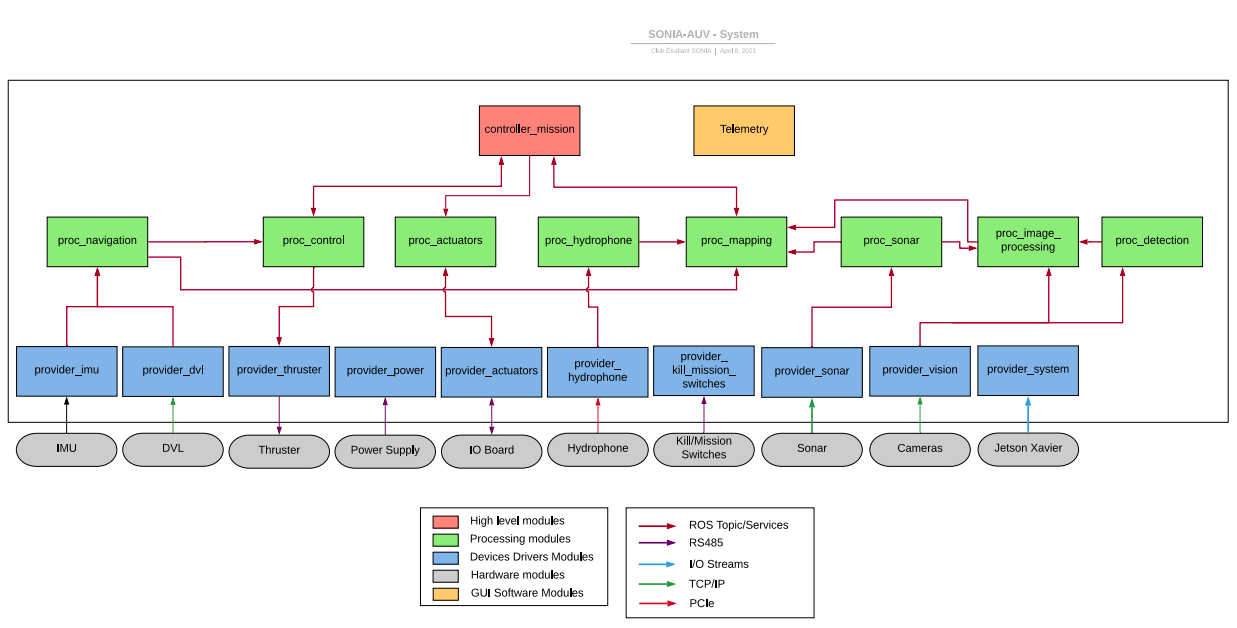
La couche des nœuds bleus est celle qui communique avec ces appareils. Par exemple, provider_thruster indique aux propulseurs la puissance qu'ils doivent produire. La couche des nœuds verts est la couche décisionnelle et envoie des informations aux nœuds bleus afin qu'ils contrôlent les périphériques externes en conséquence. En termes simples, les nœuds bleus agissent comme des traducteurs entre le niveau décisionnel et les appareils.
Cette architecture a l'avantage de permettre une amélioration et une modification faciles puisque le changement d'un équipement n'aura d'impact que sur le nœud bleu avec lequel il communique, laissant les autres couches intactes.
Galerie
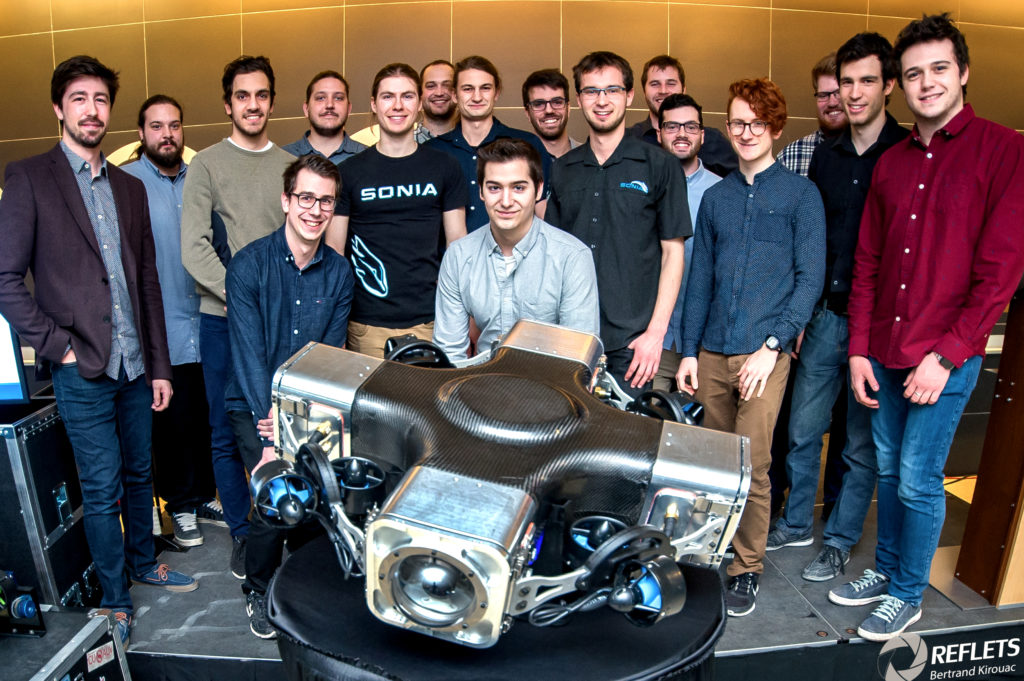
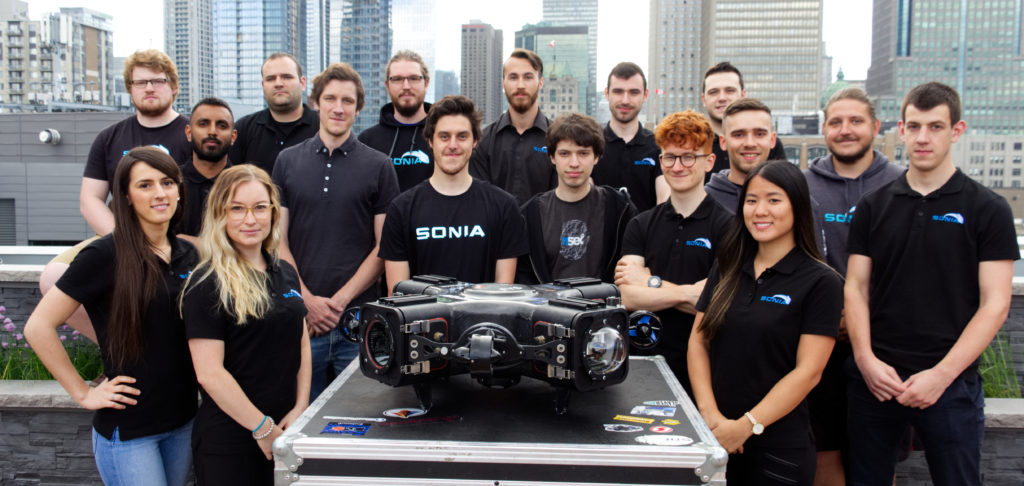
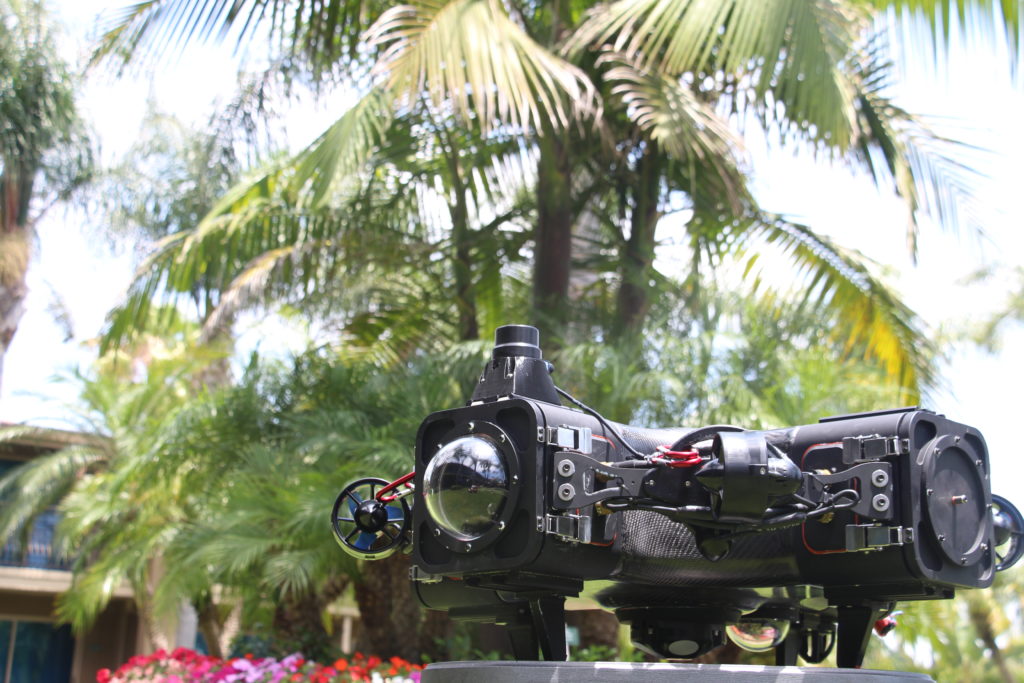
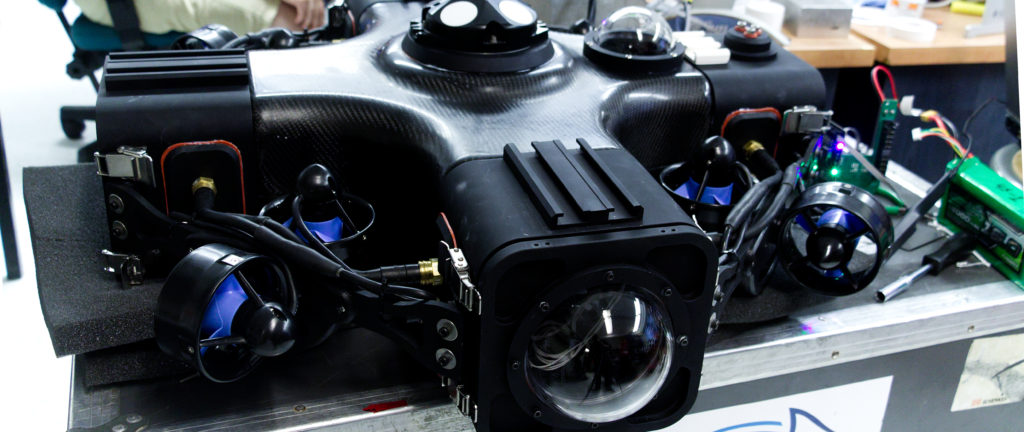
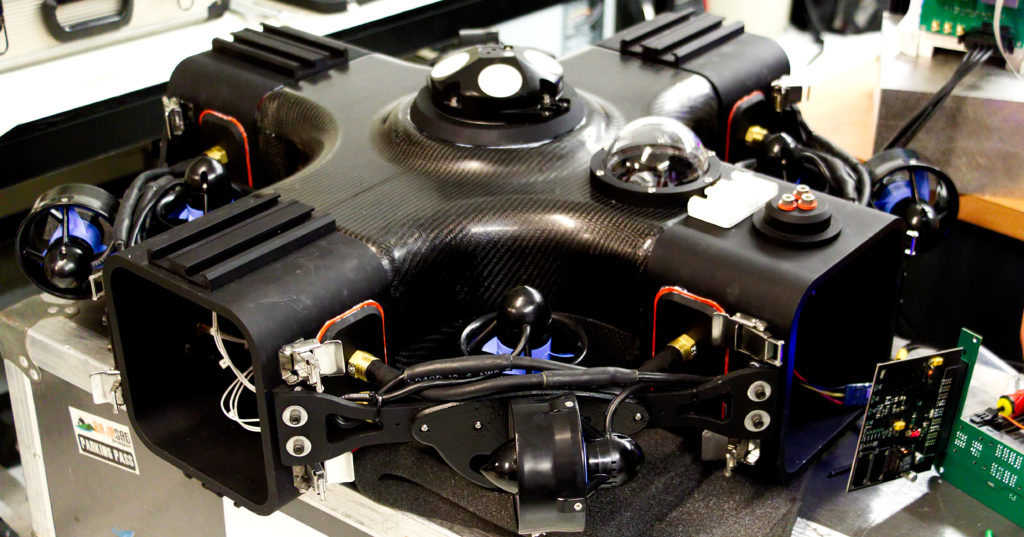
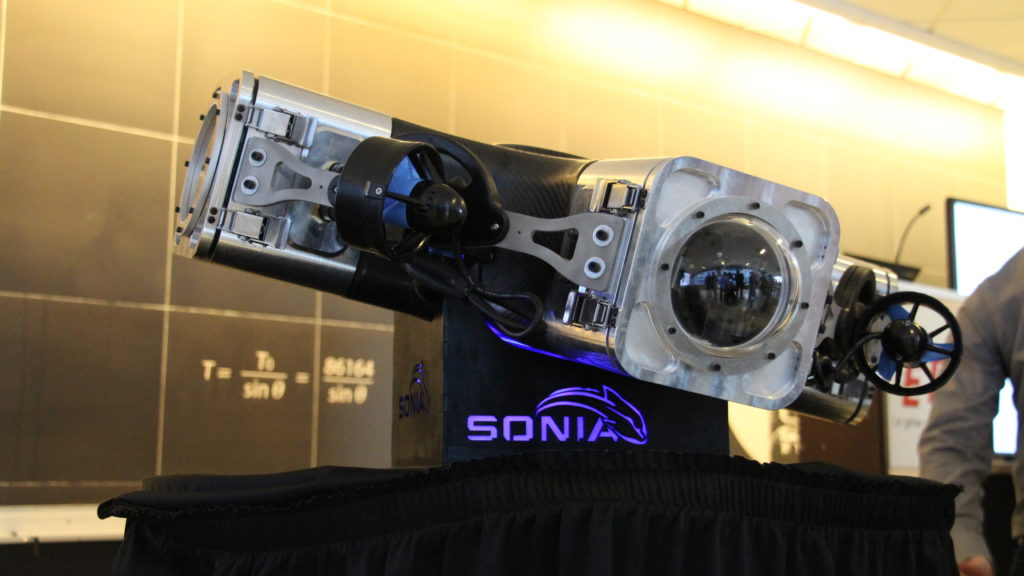
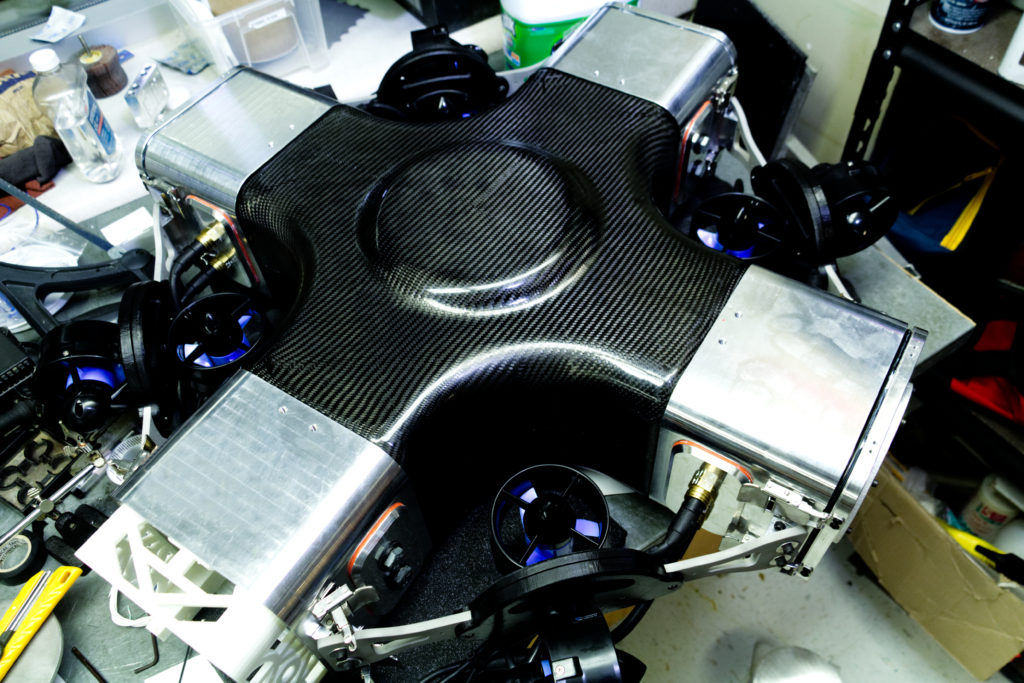
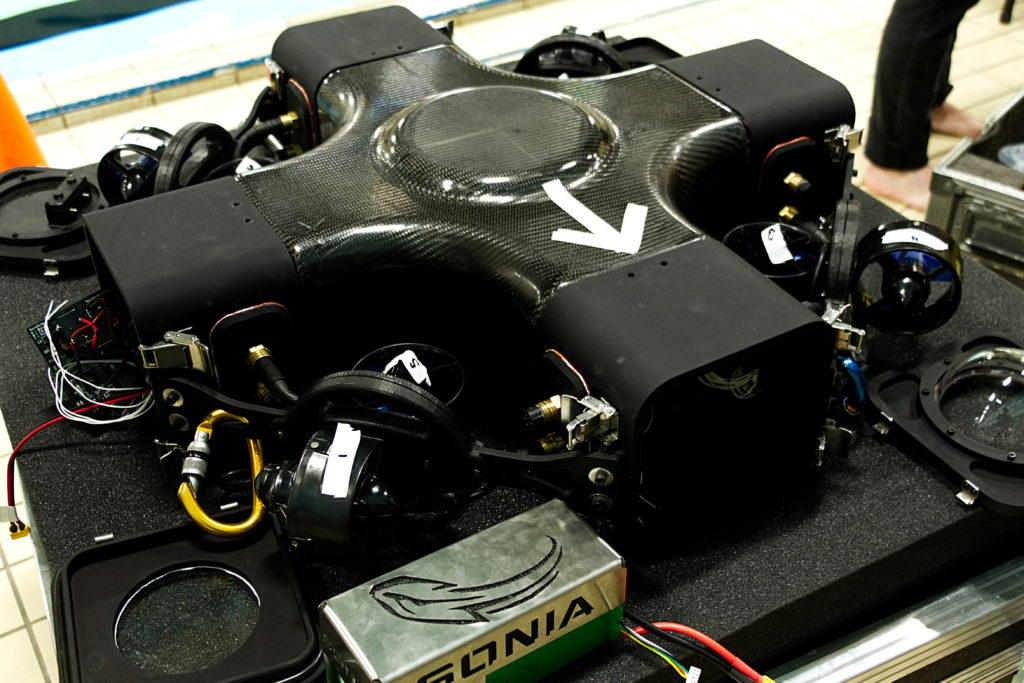
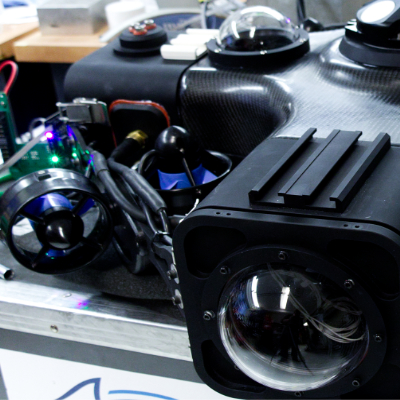
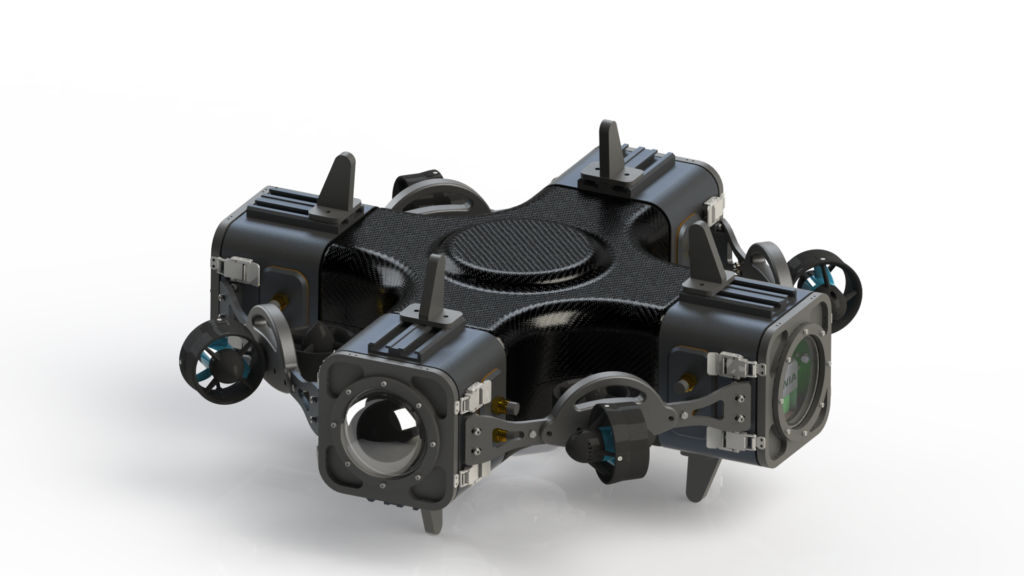
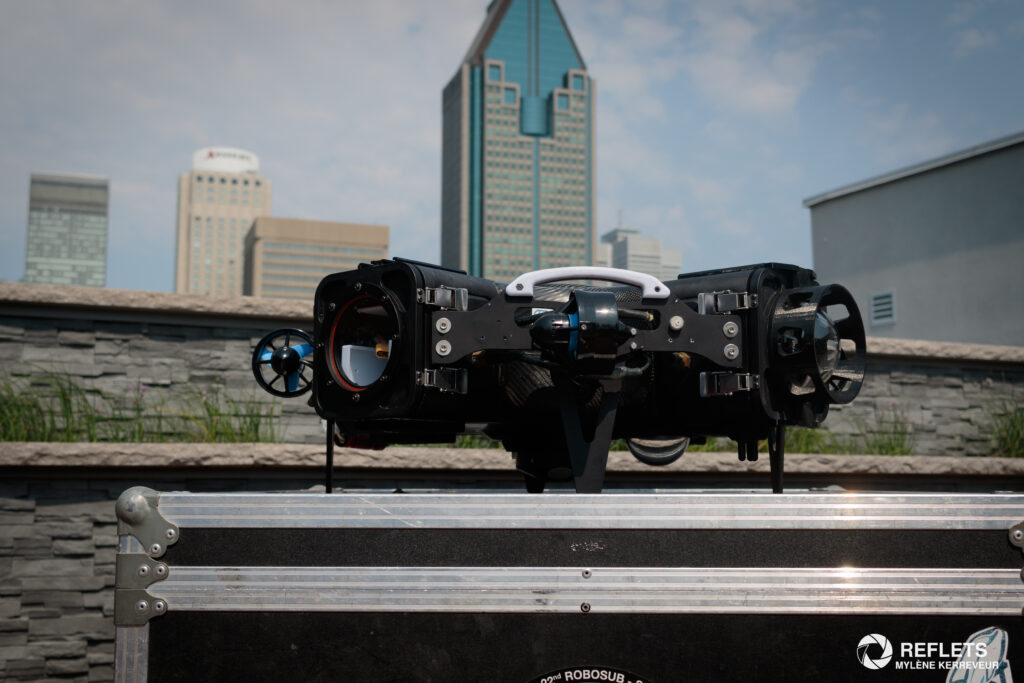
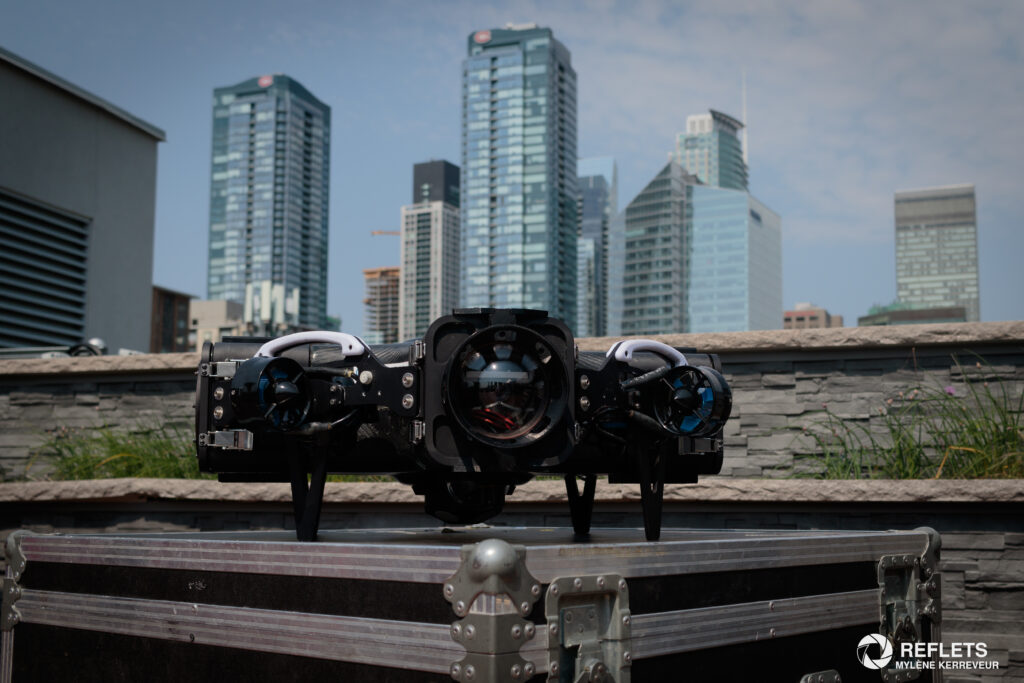